Braillo Braille vs. "Solenoid Braille"
Unique to Braillo braille embossers is that we use magnets and 168 (or 180 with our SW2 and SF2) unique embossing systems to produce our industry-leading braille, whereas all other manufacturer’s use a few solenoids. While solenoids can work for personal braille document printing (small jobs), they simply cannot handle the heavy stresses of continuous braille production – they aren’t designed to operate in that capacity.
Using magnets and having a specific, unique embossing process allows Braillo to set the industry standard, and meet all Braille Authority standards in 3 categories: braille height, braille placement and braille shape.
Braille Height
To meet these standards of a .5mm braille dot height, we use a powerful press (paper shoes) which locks the embossing pins into position before a magnet triggers each pin to be mechanically pressed into the paper using a powerful dedicated motor. Every Braillo is built with 168 embossing pins (180 for SW and SF), which means each pin has a singular purpose to create a braille dot on a single column. Braillo is the only manufacturer of braille embossers that can consistently meet .5mm braille dot heights.
All other competing embossers use solenoids, which send electricity through a thin copper coil to draw and fire a slug into paper to make a braille dot. This coil is highly susceptible to variations in the electrical charges and temperature, which means the braille pin is fired at different strengths producing inconsistent dot heights. Most competitors use between 6 and 39 solenoids to try and perform the same workload as our 168 (or 180) dedicated, and perfectly positioned embossing pins.
Braillo adheres to nearly every national braille height standard, while our competitors simply cannot.
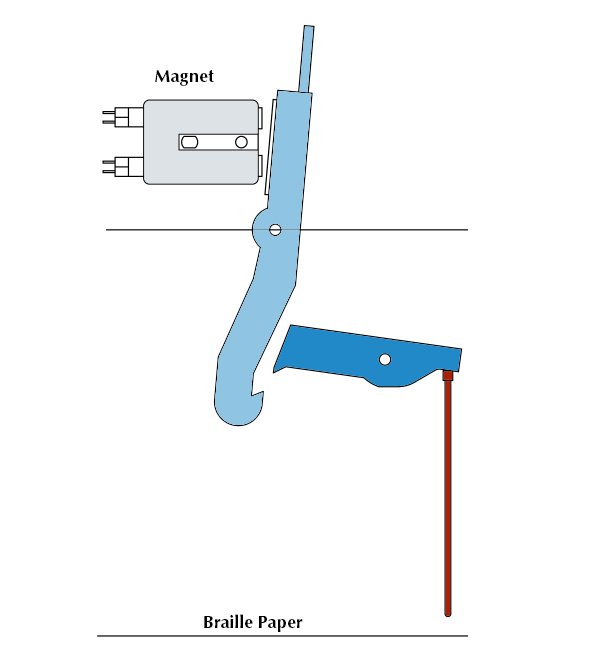
Braille Placement
Perhaps the most important aspect of quality braille that is often overlooked is dot placement. For the reader to understand what each dot represents, the dot needs to conform to an alignment of columns and rows, so that tactile patterns are recognized.
Our 168 (or 180) complete embossing systems are fixed into the paper shoes, so they can emboss an entire line of braille at one time. These fixed systems allow embossing of braille line-by-line, not dot-by-dot, ensuring that the braille dots are aligned precisely within the required braille locations.
This is not the case with solenoid-based embossers. Instead of 168 (or 180) embossing systems in a line, a solenoid embosser might use just a few solenoids (typically between 6 and 39) to do all the work. To keep pace, these solenoids must move left/right and up/down on the page to place each and every dot. This amount of motion, heat and timing inevitably leads to failures in dot placement. There is simply no possible way that a solenoid carriage can precisely line up correctly line after line, and page after page.
The Shape of Braillo Braille
The actual shape of a braille dot is what gives readers a fantastic tactile reading experience defined by clear reading and comfortable feel. The Braillo braille dot is engineered to have a crowning top with a slight ridge that gives a distinctly crisp feel, yet it is not pointy nor sharp. As you will learn, not only does Braillo have the best dot shape for reading, but due to the state of the art engineering discussed above, we are able to emboss this perfect braille shape over and over again.
As mentioned above, all other solenoid embossers are using between 6 and 39 solenoids to do the work of our 168, or 180, unique embossing systems. To keep pace, these solenoids must move left/right and up/down on the page to place each and every dot. The amount of motion that these solenoids must make in order to produce a braille dot, consistently leads to misshapen braille, as there isn’t enough time for the solenoid to firmly make a precise dot each and every time it impacts the paper. By the time it starts to make a dot, the carriage starts moving to the next location, creating irregularities.
Durability Due to Design
A production braille embosser makes millions of dots every hour and a Braillo embosser can continue this pace for 24 hours straight, day after day. The rigorous demands of production braille embossing requires the entire machine to be constructed of precision crafted parts made of high strength materials. While Braillo embossers are built to last, our competitions solenoid-based embossers cannot hold up to the demands of a production grade Braillo embosser. Take a look at the insides of a Braillo compared to our competitors and see the Braillo Difference for yourself – it is truly astounding .